CFD Software Code Application
ARA has a long history in applying aerodynamic prediction techniques (computational and other theoretical) to a range of military and civil applications.
Our strength in aerodynamics has made us the chosen partner of our customers to provide valued support to their in-house design and performance assessment teams. For several of our customers, this degree of joint working has extended over many years.
Close working with the in-house development team enables us to make technological advances and accelerate the adoption of new schemes into our CFD tools where necessary.
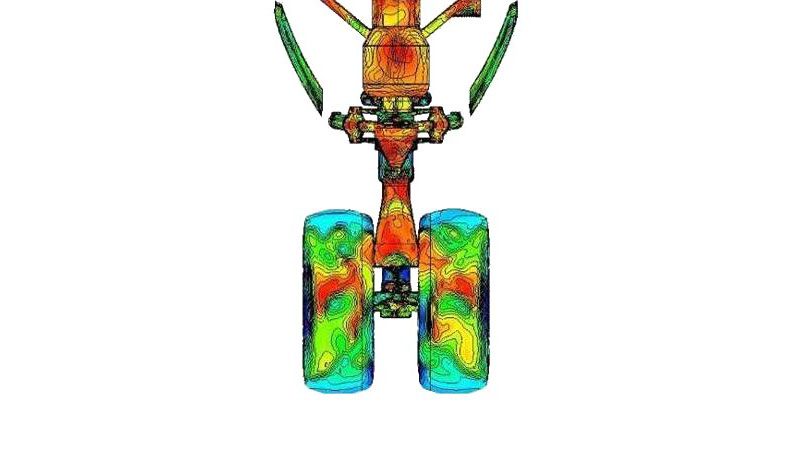
Configurations addressed recently include:
- Civil Aircraft, cruise and high-lift
- Open rotors, isolated and installed
- Manned and unmanned military aircraft
- Weapons, isolated and installed
- Landing gears
- Formula One cars and other automotive applications
The Computational Aerodynamics Applied team offers a wide-range of skills which include being able to take an application from geometry preparation to analysis and reporting.
Why ARA?
Our services include the application of ARA and commercial CFD systems. The applied services that we offer include:
- Specialist aerodynamic knowledge including aerofoils, wings, propellers
- Understanding of specialised technology, such as natural/hybrid laminar flow control
- Preparation of geometries for CFD using CAD and CAD repair tools
- Generation of meshes around complex geometries
- Use of high performance computing
- Tailored post-processing for example drag analysis or thrust/drag accounting
- Comprehensive data analysis and reporting
Intakes
Integrated CFD/Wind Tunnel
A complementary approach between CFD analysis and wind-tunnel testing can provide a cost-effective means of delivering fit-for-purpose aerodynamic data. Through its combined, specialist wind tunnel/CFD capability ARA is able to add high value to aerodynamic studies by providing this type of service.
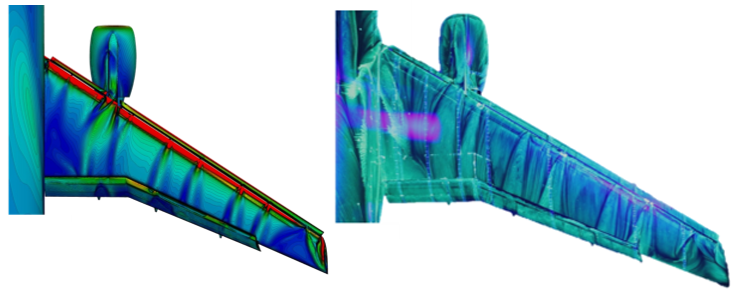
CFD can be used to:
- Assess wind-tunnel model support interference
- Design model systems for novel configurations
- Assist in the design of wind tunnel experiments
- Tailor wind-tunnel test programmes to target the most challenging conditions
- Provide post-test interpretation of unexpected wind-tunnel results
- Interpolate and extrapolate from wind-tunnel test databases
ARA has performed both wind-tunnel tests and CFD computations for numerous Customer projects over the past 30 years. One such example is the investigation the interference effect of various boom support locations on the flow over a civil aircraft empennage; the accompanying figure shows the flow field in the region of the empennage, as computed by an Euler flow solver.
Weapons and Weapon Bay Analysis
Future manned and unmanned air combat platforms are likely to make use of internal carriages for the ordinance. While providing advantages for stealth, there are a number of challenges to be overcome such as acoustic footprint, ordinance releasing and fatigue due to structural vibration.
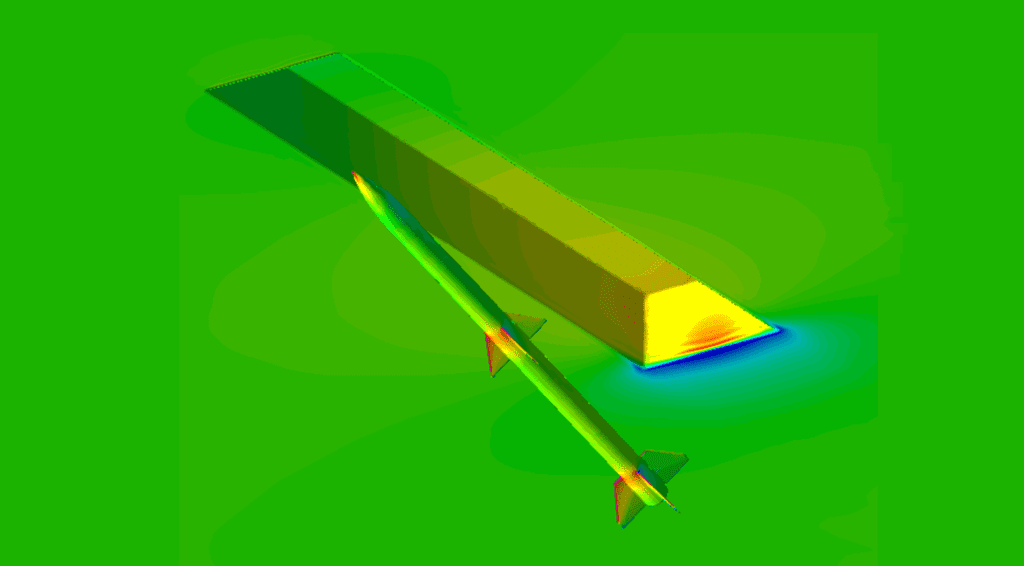
Utilising the power of ARA’s computational fluid dynamics toolset has enabled ARA to provide inputs to weapon design cycles, analysis of isolated and carriage aerodynamics, prediction of release characteristics and examination of non-conventional stores (free-to-rotate cruciform tail sections for example).
Why ARA?
ARA has a high level of experience in the accurate simulation of aerodynamic performance and the deployment of weapons from a variety of operational platforms, both of which are vital in the military sector.
Our expertise in aerodynamics (from low to supersonic speeds) and aeroacoustics allows our experts to provide specialist inputs to weapon bay analysis. ARA has been and continues to be, involved in high-level cavity research.
ARA uses a wide range of aerodynamic simulation techniques to analyse the following:
- Isolated weapon aerodynamics
- Installed weapon aerodynamics
- Weapon bay characteristics using Detached Eddy Simulations (also nose landing gear and cavity analysis)
- Gliding weapon wing design
- Inlet and duct analysis
Wing Design Process
ARA has over 30 years of experience in the area of wing design and has participated in a number of large EU funded projects researching novel aircraft design concepts and developing new CFD design tools. ARA’s bespoke CFD tools and design process are well established for clean wings and for complex multi-element high-lift configurations. Extensive laminar flow wing design experience has been applied to both high-speed jets and low-speed glider wing designs.
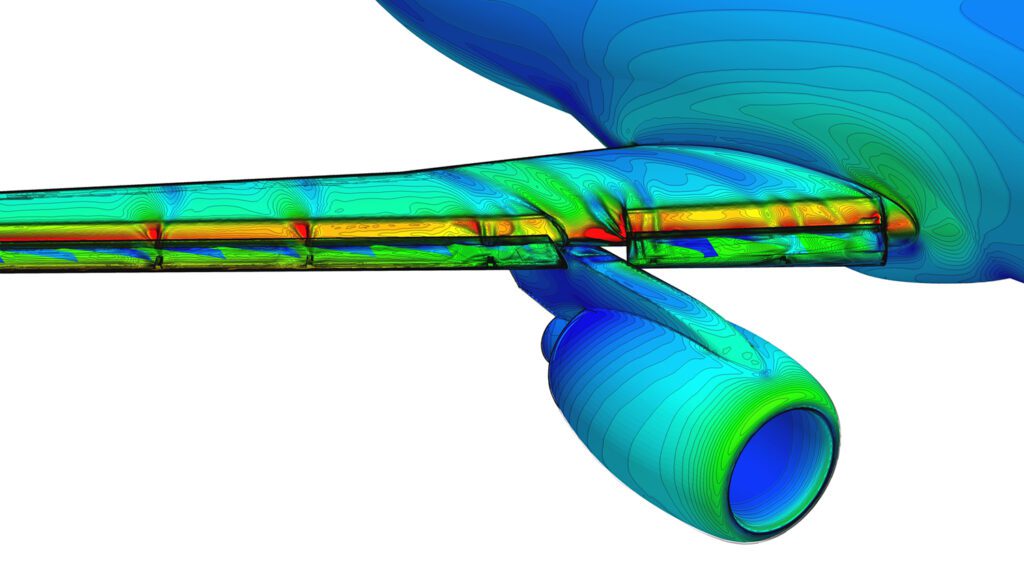
Wing section design is carried out using an ARA developed 2-dimensional screen interactive inverse design software tool, where the pressure distribution can be specified on-screen with the design software providing the corresponding geometry. This tool is combined with a highly accurate viscous-inviscid transonic aerofoil code, accurate to about 1 drag count compared to wind tunnel data. An industry-standard 3-dimensional version of the 2-dimensional aerofoil code is used for the 3-dimensional wing design and aerodynamic performance. 3-dimensional SOLAR Tau RANS simulations are used for performance analysis of the design boundaries such as CLmax.
The ability to design high-lift wings has recently been developed using an ARA 2-dimensional design tool coupled to a 2-dimensional multi-element (slat and flap) viscous-inviscid interaction (VII) aerofoil code. Multi-slotted flap configurations using either a fowler or drop-hinge system can be designed depending on the particular requirements.
Why ARA?
- High accuracy wing design tools
- Cruise wing design
- High-lift wing design
- A high level of aerodynamic wing design expertise
Wind Turbines
The aerodynamic design and analysis of wind turbines is not straightforward. Turbine blade section design is only one aspect of a complicated problem that also involves turbine array configuration, earth boundary layer effects and the aero-acoustics associated with large wind turbines. Also, the aerodynamics of horizontal and vertical axis wind turbines are by nature two separate complex problems.

ARA has a long-standing tradition of expertise in the field of aircraft propeller aerodynamic design and analysis. This expertise is used to provide the solutions associated with the complex aerodynamics associated with wind turbines.
The wind turbine design and analysis capability are built around a large amount of experience in propeller aerodynamics at ARA and CFD tools developed to provide the high-quality data required by the customer. This can range from blade section design to evaluating design changes on specific areas of the turbine by generating and providing the client with all the aerodynamic data for decision-making, to having a major involvement in the design and development of areas of the turbine by contributing our own experience in aerodynamics and fluid mechanics.
With the wealth of CFD process development and aerodynamic analysis experience available, ARA is able to provide specialist input into wind turbine blade aerodynamic design technology to match the demands of the renewable energy industry to maximise the potential of energy generation by wind turbines.